In the calcium carbonate powder processing industry, 800-mesh ultrafine powder is highly sought after for its wide range of applications, such as toothpaste, rubber, coatings, and more. However, one of the most critical concerns for businesses investing in production is how to scientifically control the per-ton production cost of 800-mesh calcium carbonate powder. This article will analyze the key factors influencing costs from multiple perspectives and explore how to reduce expenses and improve efficiency through optimized processes and equipment selection.
1. Raw Material Costs: The First Barrier from Ore to Powder
The quality of raw materials directly affects processing efficiency and product value. High-whiteness (≥94%) calcite or marble with low impurity content is ideal for producing 800-mesh calcium carbonate powder. If the raw ore contains excessive iron or moisture, additional pre-processing steps (e.g., crushing, drying) are required, increasing equipment investment and production time, thereby raising costs indirectly. Additionally, transportation expenses and fluctuations in ore procurement prices must also be factored into the overall cost calculation.
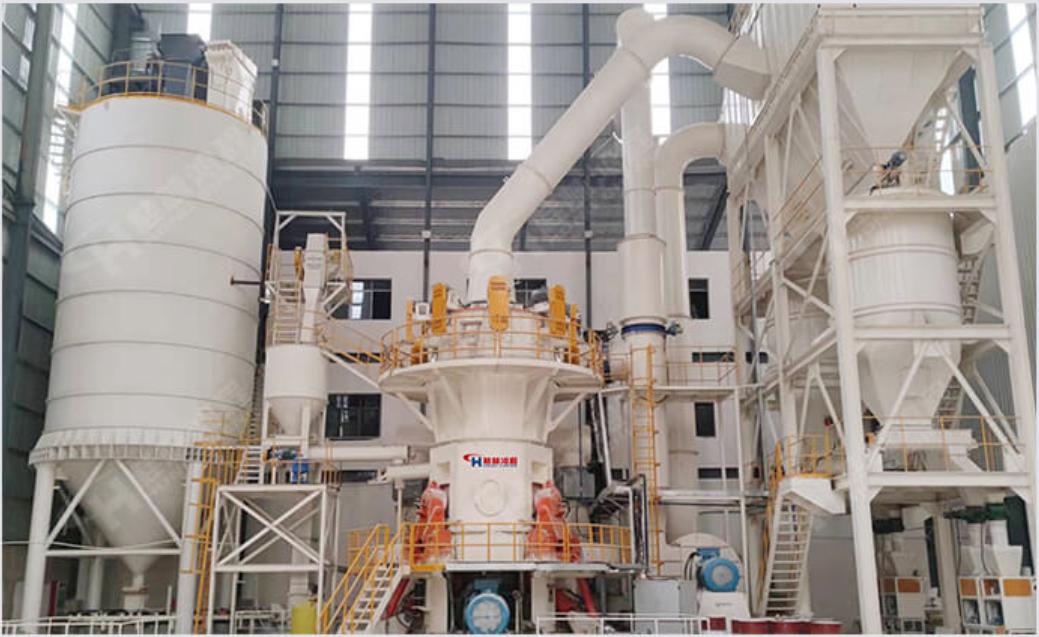
2. Equipment Selection: Balancing Energy Consumption and Efficiency
Production equipment is the core factor in cost control.
Traditional ball mills consume up to 120 kWh per ton, whereas ultrafine vertical roller mills (e.g., HLMX series) utilize roller-pressing grinding technology, reducing energy consumption to below 90 kWh per ton while achieving a single-unit output of 4-40 tons/hour, significantly lowering electricity costs.
For example, in a 50,000-ton annual production line, adopting high-efficiency vertical mills can save hundreds of thousands of yuan in electricity costs per year.
Other factors like wear-resistant part lifespan, automation level (e.g., full-automatic control reducing labor input), also directly impact maintenance and labor costs.
3. Process Design: The Hidden Lever of Fine-Tuned Management
A scientific process design can significantly optimize cost structures, such as:
Grading System Optimization: Multi-stage classification reduces recycling rates, improving first-pass yield and avoiding energy waste from repeated grinding.
Production Line Layout: Rational equipment sequencing (e.g., crushing-grinding-classification integration) shortens material flow paths, reducing handling losses.
Environmental Investment: While high-efficiency dust collectors increase initial costs, they prevent environmental fines and enhance workshop stability, proving more economical in the long run.
4. Economies of Scale & Operational Management: The "Amplifier" of Cost Reduction
Larger production scales lead to lower per-unit costs.
For instance, a 120,000-ton/year heavy calcium carbonate project using HLMX ultrafine vertical mills achieved a 15%-20% lower per-ton cost compared to small and medium-sized production lines.
Additionally, intelligent operations (e.g., remote monitoring, preventive maintenance) minimize downtime, ensuring high capacity utilization and further reducing fixed costs.
5. Regional Policies & Energy Prices: External Variables That Matter
Industrial electricity prices and environmental subsidies vary greatly by region.
For example, operating equipment during off-peak hours can reduce electricity expenses, while some regions offer tax incentives for green manufacturing projects, indirectly lowering overall costs.
Enterprises must adjust production strategies dynamically based on local policies.
Conclusion: Accurate Cost Calculation Requires Customization
The per-ton cost of 800-mesh calcium carbonate powder is not a fixed value but a dynamic result influenced by raw materials, equipment, processes, scale, and other intertwined factors.
For example, Guilin Hongcheng’s HLMX ultrafine vertical mill users report achieving 30% lower energy consumption and 25% higher output through customized solutions.
To obtain a precise cost analysis tailored to your ore quality, production needs, and regional policies, we recommend consulting Guilin Hongcheng’s professional engineering team.
Phone:0086-15107733434
Email:hcmkt@hcmilling.com
Post time: Apr-24-2025